Buildings occupy a central position in much of our work – most of what we do as landscape designers is affected in one way or another. I started this short series because I felt that whilst there was a lot written about the generalities (urban design, cityscape etc.), there is surprisingly little written about the ‘specifics’. Roof gardens seemed the natural place to start. In the last post – Roof Garden Design: #1 Exposure and Screening – I explored the unique microclimate of rooftop spaces and what mitigation strategies are available to us as designers. In the next article I will look at another aspect of the cultural properties of these spaces – water; but before we get on to that, there is another more basic issue (literally) to deal with – the roof itself.
When I first started out practising in landscape design about thirty years ago, I was frequently asked to look at roof terraces on older, existing buildings. The first question I always used to ask was what the roof structure was made of (translating to what load it might be able to take). Clients frequently didn’t know and were sometimes a little dismissive of the necessity for care here. As we were generally standing in the centre of their roof space, I would conduct a simple test: I would make a small jump into the air. I weigh getting on for fourteen stone (about 87kg or 190lbs).
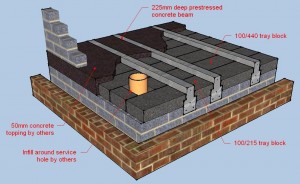
Typical beam and block construction (courtesy of carter-concrete.co.uk)
The small jump allowed me tell instantly whether I was on a timber roof (which would flex alarmingly), a lightweight concrete structure such as beam and block (which had a small but discernible flex) or a loadbearing concrete slab (which would not noticeably flex at all). On timber roofs, a look of alarm used to spread across the client’s face, which was as good a demonstration as any other of the need to take load bearing ability of the structure seriously!
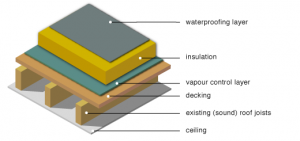
Typical timber roof construction (image courtesy of greenspec.co.uk)
Of course, this is no substitute for proper calculation and advice from a qualified engineer, but it is a starting point in knowing what sort of load the roof is likely to be able to withstand. On new buildings, it is generally possible to get information from the structural engineer as to what load the roof has been designed for. This will generally be expressed in kilonewtons (kN). One kilonewton roughly translates into 100kg of force-load, so 4.5kN/m2 designed load approximately equates to a 450kg load per square metre. Engineers often make an allowance for live load on top of self-weight or dead load, to take account of the weight that people, furniture etc. exert. So in calculating paving weights this has to be maintained, but for larger freestanding planters, these can (with the engineer’s approval) include the live load allowance. Note that the calculations need to allow for wet compost and the weight of the plant itself rather than dry compost. Most structures can take more weight around the perimeter than in the centre, but be particularly careful on structures of a beam construction to find out which direction the beams run in. It is possible to safely load quite heavily across the ends of a number beams, but is dangerous to load along the length of a single beam, even if it is along the edge of the terrace.
The state of the waterproofing is also very important: there is little point in starting out on an expensive roof terrace if the waterproof membrane is old and in need of renewal. This needs to be tackled first by the client. There are many different systems of water proofing. On larger roofs it is common to use hot-melt continuous systems. On smaller roofs these are not always economic, although there are traditional asphaltic systems. I would also recommend that a root barrier is installed. Roots can attack organic compounds such as asphaltic roofing or mineralised felt. Even if the membrane is a continuous sheet, roots exploit weaknesses and joints which can cause leaks in the future. Chemical root barriers are therefore better than physical ones. Most roof companies have a standard product for just this sort of situation, but if not, lay a proprietary product above the drainage layer, such as RootX, which is copper foil sandwiched between geotextile (www.water-lines.co.uk/rootx) before proceeding with the rest of the build-up in planted areas.
Most roofs these days are ‘warm roofs’, meaning that the insulation is above the roof structure rather than below. On larger roofs it may be covered by a thin concrete layer, but frequently the insulation needs to be held in place by the layers above. In the next post, I will explore some of the options in terms of build-up, as well as looking at drainage and irrigation. In the meantime, as always if you have any questions (or criticisms!) leave a note below.